Pokretni regali predstavljaju inovativno rešenje u skladištenju, ističući se svojom konstrukcijom sličnom nepokretnim regalima. Sigurnosni uređaji, poput mikroprekidača i beskontaktnih elektromagnetnih davača, obezbeđuju bezbednost i automatsko zaustavljanje u slučaju prepreka, čineći pokretne regale pouzdanim rešenjem za skladištenje robe.
Sistem sadrži sigurnosne uređaje koji nailaskom na prepreku aktiviraju mikroprekidače i zaustavljaju rad pogonskog mehanizma. Zaustavljanje regala pri dolasku do pomerenog regala je izvedeno beskontaktnim elektromagnetnim i svetlosnim davačima.
Radi boljeg razumevanja, sagledajmo troškovnu analizu tri paletna sistema ugrađenih na prostoru istih dimenzija:
Standardno regalno skladište
- Troškovi izgradnje: 550.000 evra
- Paletni regali 6 nivoa: 28.000 evra
- Viljuškar: 30.000 evra
- Ukupni troškovi: 608.000 evra
- Iskorišćenje prostora: 43 %
- Kapacitet: 912 paletnih mesta
- Troškovi po paletnom mestu: 667 evra
- Troškovi izgradnje: 600.000 evra
- Troškovi tačnosti nivoa: 20.000 evra
- Paletni regali 9 nivoa: 45.000 evra
- Viljuškar: 80.000 evra
- Standard DIN 15185: 10.000 evra
- Ukupni troškovi: 755.000 evra
- Iskorišćenje prostora: 47 %
- Kapacitet: 1494 paletnih mesta
- Troškovi po paletnom mestu: 505 evra
Skladište sa pokretnim regalima
- Troškovi izgradnje: 300.000 evra
- Ugradnja šina u pod: 9.000 evra
- Paletni regali 6 nivoa: 260.000 evra
- Viljuškar: 30.000 evra
- Ukupni troškovi: 599.000 evra
- Iskorišćenje prostora: 70 %
- Kapacitet: 1488 paletnih mesta
- Troškovi po paletnom mestu: 402 evra
Mitovi o pokretnim regalima
Mit 1: Pokretni regali su skupi. Pošto pokretni regali stvaraju kompaktni skladišni sistem, investicija se brzo vraća. Ovaj sistem omogućava direktan pristup svakoj paleti u skladištu. Regali su instalirani na osnovi, pa se otvaranjem odgovarajućeg prolaza dolazi do željene palete. Visoka iskorišćenost raspoloživog prostora postignuta je usled povećanog skladišnog kapaciteta i smanjenja potrebnog prostora za gradnju.
Mit 2: Pokretni regali su pogodni samo za hladne komore. Ovi sistemi se ne koriste samo u hladnjačama i ostalim temperaturnim uslovima. Šta više, idealni su za robu široke potrošnje, sirovine, carinska skladišta, uslužna skladišta, konzolna skladišta za drvnu i papirnu industriju, skladišta za šipkaste proizvode i limove itd.
Njihova upotreba u hladnim prostorima je neprikosnovena jer izrazito smanjuju prostor za hladjenje, samim tim i troškove hladjenja.
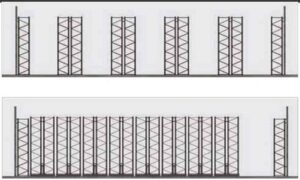
Slika gore ilustruje značajno povećanje kapaciteta koje obezbeđuje sistem pokretnih regala (od 80 do 120 više paleta od klasičnog skladišta u datom primeru). Stepen povećanja zavisi od vrste korišćenog viljuškara i veličine prostora.
Mit 3: Služe samo za povećanje kapaciteta skladišta. Pokretni paletni regali se mogu upotrebiti i za projekte smanjenja skladišnog prostora za isti kapacitet skladištenja. Ova karakteristika je naročito pogodna kada kompanija zakupljuje fizičke objekte – skladišta i sama ih oprema paletnim regalima. U tom slučaju je moguće smanjiti troškove zakupa na pola.
Mit 4. Ugradnja sistema pokretnih regala je komplikovana. Pokretni regali se mogu ugraditi u skladište u toku gradnje novog objekta, ali se mogu lako postaviti u već postojeća skladišta. Potrebne su određene intervencije u podu skladišta, čija složenost zavisi od vrste, kvaliteta i nosivosti postojećeg poda. Takođe se postojeći statični paletni regali mogu transformisati u pokretne.
Mit 5. Pokretni regali su pogodni samo za velike projekte. Pokretni regali, pored primene za skladištenje svih vrsta paletizovane i gabaritne robe, idealni su i za odlaganje – arhiviranje dokumentacije, knjiga, papira, obrazaca, prospekata, filmova itd, gde se ručno opslužuje i gde je mala frekvencija ulaza i izlaza uskladištenih jedinica (M. Georgijević, Regalna skladišta, 1995).
Takođe je poznata i njihova pogodnost za skladištenje pneumatika, pre svega kod proizvođača i distributera, gde se na malom prostoru može držati velika količina pnuematika svih vrsta i namene.