Komisioniranje je aktivnost koja zahteva najviše rada u svakom skladištu i distributivnom centru i na koju odlazi više od 63% troškova skladištenja. U cilju da pruži zadovoljavajuće performanse, metod komisioniranja mora biti prilagođen poslovnim operacijama kompanije.
Kako je smanjenje troškova i povećanje produktivnosti postalo uslov za opstanak i konkurentnost poslovnih sistema, komisioniranje, kao najzahtevnija operacija u skladištu, došlo je u žižu interesovanja, kako logističkih profesionalaca, tako i top menadžera kompanija. Komisoniranje – proces uzimanja artikala sa skladišnih lokacija u cilju ispunjenja specifičnih porudžbina kupaca – zahteva najviše fizičkog rada u skladištima sa ručnim sistemom i veliko ulaganje kapitala u skladištima sa automatizovanim sistemom. Iz tih razloga, logistički eksperti smatraju da je komisioniranje oblast sa najvećim prioritetom za promene i poboljšanja.
Nekoliko trendova u proizvodnji i distribuciji doprinelo je popularnosti komisioniranja. U proizvodnji, naglasak je na manjim serijama, isporukama direktno kupcima, smanjenju vremenskih ciklusa. U distribuciji, u cilju da opsluže klijente, kompanije prihvataju kasne narudžbe, obezbeđujući brzu i pravovremenu isporuku u dogovoreno vreme. Veliki broj manjih skladišta je zamenjeno jednim većim distributivnim centrom u cilju smanjenja troškova i veće produktivnosti. Takođe, sve je više zastupljeno dodavanje vrednosti proizvodima u samim skladištima, poput etiketiranja, pakovanja i paletizacije) što još više doprinosti složenosti skladišnih operacija. Tome treba dodati i povratnu logistiku, gde je uloga skladišta takođe ključna.
Organizacija operacija komisioniranja ima direktan uticaj na poslovanje distributivnih centara, a samim tim i na performanse lanca snabdevanja. Od vremena kada je nalog stigao u skladište, do trenutka isporuke kupcu, postoje velike mogućnosti za greške u tačnosti i kompletnosti naloga, da ne pominjemo kašnjenje isporuke. Međutim, postoji i prostor za poboljšanja.
Sistemi komisioniranja
U jednom skladištu se mogu naći različiti sistemi komisioniranja. Većina kompanija koristi ljude za komisioniranje u sistemu čovek ka artiklu, gde radnik hoda po skladištu, traži i prikuplja potrebne proizvode.
Postoji nekoliko organizacionih varijanti ovog sistema. Osnovne varijante su komisioniranje po jednom nalogu i komisioniranje više naloga. Mogu se organizovati veći broj međuvarijanti osnovnih modela.
Drugi sistem je artikal do čoveka, gde uglavnom skladišne dizalice dovoze kutije sa artiklima do radnika, koji uzima potrebnu količinu, a dizalica ostatak vraća na lokaciju. Dizalica može raditi u singl, dualnom i multiplikovanom komandnom režimu. Osim dizalice, artikle do radnika mogu donositi i drugi automatizovani sistemi, poput vertikalnih liftova, vertikalnih ili horizontalnih karusela.
Komisioniranje se može obavljati uz pomoć vozila – viljuškara, kolica ili uz pomoć konvejera – valjkastog ili nekog drugog transportera.
Tehnologije komisioniranja
Izbor tehnologije komisioniranja zavisi od toga kolika nam brzina komisioniranja potrebna u celom skladištu ili pojedinim skladišnim zonama. Slično sistemima, u jednom skladištu mogu postojati različite tehnologije.
Različite tehnologije pružaju različite brzine komisioniranja. Naredna tabela nam može pomoći da izaberemo tehnologiju za pojedine skladišne zone ili određene artikle.
Za artikle iz grupe A, koji imaju veliku izlaznost iz skladišta može se koristiti automatizovana ili poluautomatizovana tehnologija komisioniranja koja pruža izuzetnu produktivnost od 600 do 1200 stavki na sat. Za tu svrhu se mogu koristiti komisioni roboti itd.
Takođe za grupu A artikala, visoku produktivnost, od 300 do 700 stavki na sat omogućava tehnologija horizontalnih karusela koji su povezani sa ERP-om uz pomoć sistema za upravljanje skladištem.
Pick to light sistemi omogućavaju komisioniranje do 400 stavki po radniku na sat. Velika brzina ovog sistema je idealna za primenu na artikle iz grupe A i B.
Vizuelno komisioniranje staje rame uz rame sa glasovnim komisioniranjem. Glasovno komisioniranje je tehnologija gde računar glasom usmerava radnika gde da se kreće, koje artikle da pokupi, koliko njih i gde da ih odnese. Vizuelno komisioniranje je tehnologija gde radnik vidi na ekranu ručnog računara kako izgleda artikal koji treba da uzme, kao i njegovu lokaciju.
Komisioniranje uz pomoć ručnog računara je modernija verzija tradicionalnog odvajanja artikala gde radnik sa papira čita koji su artikli potrebni i eventualno gde se nalaze. Kada nadje artikal, često mora i na magacinskoj kartici da unese promene. To je sada zamenjeno ručnim računarom uz pomoć koga radnik skenira lokaciju, skenira artikal i tako automatski apdejtuje stanje zaliha.
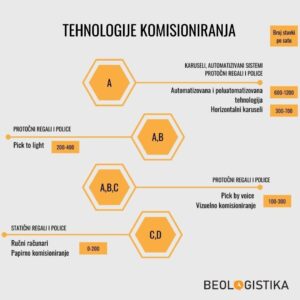
Zbog niske produktivnosti, ova dva načina komisioniranja treba koristiti samo za artikle koji imaju malu izlaznost iz skladišta.
Čovek ka artiklu
Obratićemo više pažnje sistemu gde radnik hoda po skladištu i traži potreban artikal jer je taj sistem najzastupljeniji kod nas.
Na tržištu se nude sve tehnologije koje podržavaju ovaj sistem, a komisioniranje uz pomoć ručnih računara se već odomaćilo u našim skladištima i distributivnim centrima.
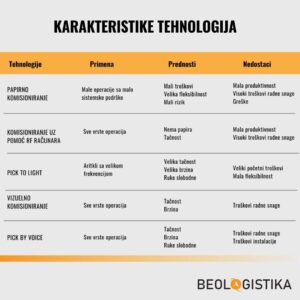
Zaključak
Poboljšanja koja kompanija može uvesti u skladišne operacije bez primene tehnologije su veoma slaba. Na proces komisioniranja treba primeniti sve poznate organizacione metode poboljšanja produktivnosti, ali bez uvođenja savremenih tehnoloških rešenja rezultati su uvek nezadovoljavajući. Međutim, uvođenje tehnologije u skladište zahteva veliku opreznost i ogromne pripreme, koje se pre svega odnose na izbor prave tehnologije.
Najčešći izbor tehnologije kompanije vrše na osnovu vremena povratka investiranja. Ukoliko će odabrana tehnologija smanjiti radnu snagu za 10 ljudi i smanjiti greške komisioniranja za 30 %, godišnja ušteda za firmu bi bila oko 8,5 miliona dinara. Ukoliko je za firmu prihvatljiv povraćaj investiranja za 2 godine, onda je cena od 17 miliona dinara za implementaciju odabrane tehnologije potpuno realna.
Pre izbora prave tehnologije velika uloga je na menadžerima logistike i skladišta, od kojih se očekuje temeljna analiza brojnih faktora u vezi sa proizvodima, kapacitetima i zahtevima tržišta. Nije svaka tehnologija prihvatljiva za svako skladište. Takođe, relativno nepoznate tehnologije sa više automatizacije donose znatne prednosti i veće uštede iako su početna ulaganja nešto veća.
U svetu je sve više popularna modernizacija skladišnih operacija u dve faze. Ukoliko je krajnji cilj potpuna automatizacija, u prvoj fazi uvodi se tehnološko rešenje koje će odmah doprineti produktivnosti i efikasnosti i biti osnova za automatizaciju. Na primer, uveđenje WMS-a može biti prvi korak ka automatizaciji.
Tekst je objavljen u časopisu Poslovna logistika, februara 2012. godine.